Details
Motivation
Approach
Objective
No experimental data has been obtained for a Pulsed Combustor Ejector Shroud system (PCES) operating in gas turbine relevant conditions (i.e. elevated pressure).
Also, little experimental data exists detailing PCES pollutant emissions (NOx, CO, UHC), none at relevant pressures. For this reason, the objectives are:
Experimental Apparatus
-
Pressure-gain combust or experimental apparatus is composed pulsed-combustor coupled with an unsteady ejector and enclosed within a shroud
-
High-pressure shroud is capable of sustained operation at 10 bar, with 0.5 kg/second of inlet air
-
Apparatus allows for characterization of the pressure-gain combustion system in simulated gas turbine conditions through measurement of
the total pressure ratio across the heat addition process as a function of the total temperature ratio
-
Initial experiments will be conducted with gaseous fuels with the final objective of moving to liquid transportation fuels.
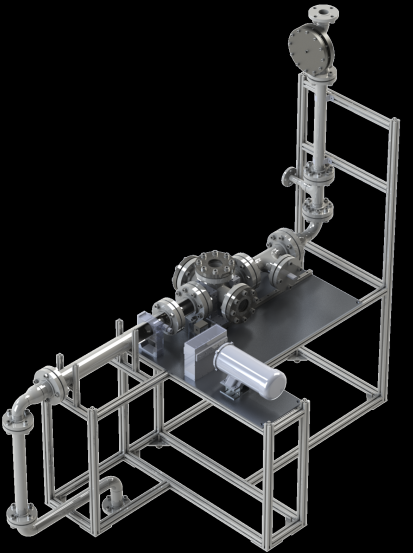
Figure 1: High pressure shroud for pressure gain combustor characterization

Figure 2 : High pressure shroud for pressure gain combustor characterization
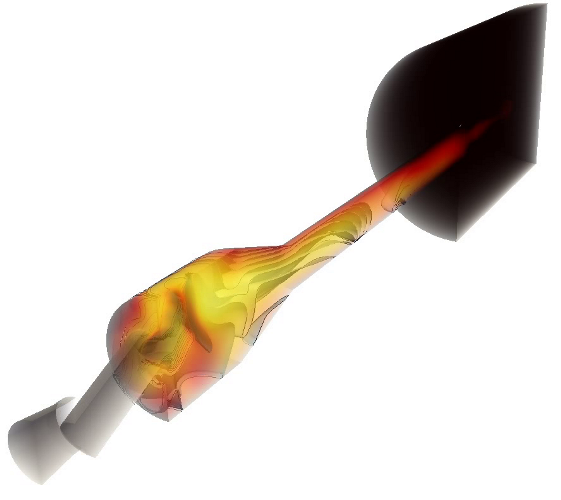
Figure 3 : Volume rendering of temperature with fuel mass fraction isocontours